ROLL BOND EVAPORATORS
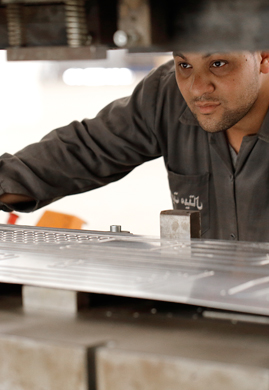
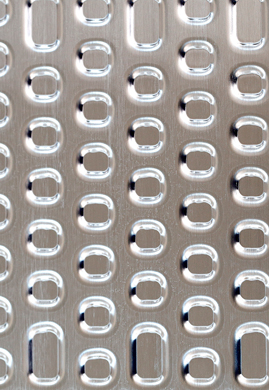
Roll Bond Evaporators in BRIGHT METAL is a new player in the production of roll bond plates. Our roll bond line comes from Chambery, France and was developed as state-of-the-art of Pechiney, recently acquired by Alcan. After the Italian Compagnia Generale Alluminio Spa (CGA) -last operative owner of Rubanox, ended the activity in France, the line stopped for a period of time.
A new life came to the line when BRIGHT METAL decided to invest in this activity moving the line from France to Egypt. A professional and detailed restructuring job was done to restart the line and produce again the high quality that was well known and appreciated in the market.
In order to maintain that high quality, BRIGHT METAL has formed a team with old and new operators to transfer the knowledge and know-how to a new generation of technicians.
PRODUCT CHARACTERISTICS
Dimension
- Length max/min : 2500/200mm
- Width max/min : 600/150mm
Alloys
Aluminium Al1050
Alloy (Flat side) Al8006 & Al3003
Inflating
DSI (Double Side Inflated)
OSF (One Side Flat, the other one is inflated)
OSFX (OSF with not inflated side extra flat)
Rolling tollerances
- 1,5% elongation and 1,5° out of square
FIELDS OF APPLICATION
Domestic and Commercial Refrigeration
- Evaporators for static refrigerators and freezers
- Condensers
Thermodynamic Heat Pumps
- Solar Evaporators
- Condensers for boilers and water tanks
Climatization
- Radiant ceilings
- Radiant walls
Electronics and Automotive
( Electric Vehicles )
- PCB cooling frame
- Box water cooling
- Battery cooling
- Surface heat exchangers
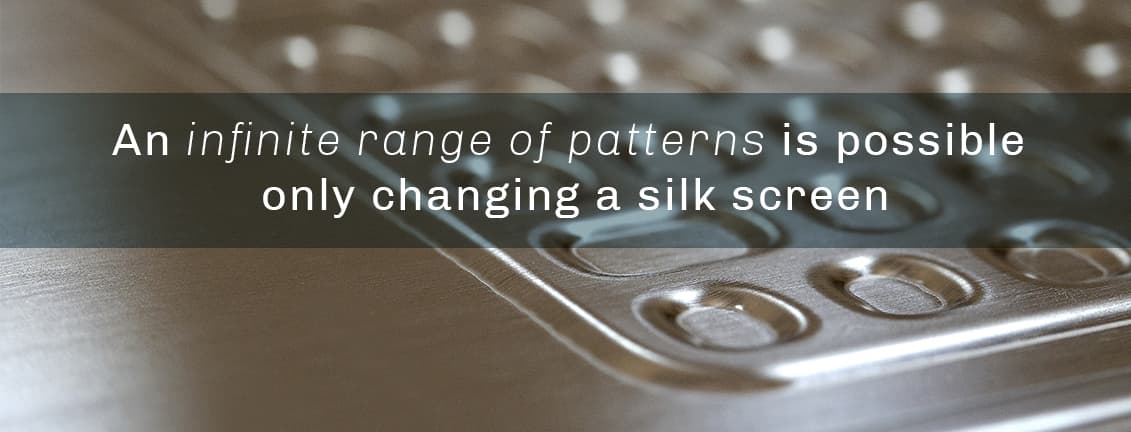
PRODUCTION STEPS

Please fill in this form if you have any inquiries and we will reply to you as soon as possible.